How can we help you realize your goals?
Qualified consulting every step of the way
-
Working closely with our partner, we outline a preliminary definition of the product and its functional requirements. This outline includes proposed architecture and specifications for the basic hardware, input/output types, functions, displays and interfaces.
In addition to this we estimate a pricing scheme for development tests and production units as well as a preliminary timetable. In the event of radically new design principles and functions we will test them in a prototype environment for realization evaluation. The step is concluded with your decision to continue to the next step or to set the process on hold.
-
In close cooperation, we analyze the machine as well as the desired working procedures. Our practical and creative design engineers will then present a description of the proposed solution, based on the joint discussion, the technical possibilities, and the ideas.
We adjust the timetable, and the project expenditure is estimated in further detail and if required a fixed price is given.
The step is concluded with your approval and accept of the product specifications.
-
We design and program the required software applications to meet the exact operating concept and service in the end product specifications. This step potentially includes development of formulars and definitions of interfaces and protocols.
If customized hardware is required, then we develop it at this stage. Depending on degree of customization electrical layout, component selection and pcb design as part of this sub process.
When hardware and software designs are approved, we manufacture a prototype. A system testing method is established to ensure that sequences and programmes are fully integrated and perform to your requirements.
-
We subject every single control solution to thorough quality and prototype field tests to ensure that the final solution is in line with or exceeds expectations.
This step includes prototype testing, module testing and system testing. Technical specifications are updated, report and technical manuals are completed.
-
We make the final adjustments according to the test results in the previous phase. Previous phases can be repeated as specifications may change during the ongoing development process in order to optimize the end product further. It is imperative for the best end result that changes are handled in a unbureaucratically manner.
We complete functionality and all specifications are approved by you. The parts list is revised and completed. Internal test documentation and manufacturing documentation is completed. And then we construct the manufacturing tools and equipment.
-
When you are completely satisfied with the end product, we put it into mass production. As many production processes are performed in-house, it’s possible to operate with a high degree of flexibility regarding modifications and delivery schedules – while maintaining a stringent quality control.
We initiate 0-series production and supervision of production flow is carried out. The first end-user applications are implemented, tested and feedback from end-users is evaluated. The product is approved for release and production. And the feedback is logged as input for upcoming product revisions.
-
Ongoing evaluation is an important part of any Lykketronic development process. We want to ensure that our solution has in fact realized its expected potential. We continuously follow up on deliveries and potential improvements.
We continuously evaluate on-time delivery, warehousing, service and support requirements and other customer related issues in close cooperation with the customer. Meetings concerning product evaluation and follow-up are carried out and next generation of the product solution is prepared.
-
Before, during and after a development process or after providing a standard product solution, our experienced service and support technicians stand by you. We are ready to help you with qualified answers to specific questions and in-depth implementation advice to ensure that your solution is integrated correctly and running smoothly.
We support OEMs throughout the world – with minimum delay. Having production facilities and technical competences in-house provide our partners with multiple benefits – for example, if spare parts, extra components, etc., are needed, we provide them with minimum delay – minimizing service- and downtime.
Furthermore our remote service and support capabilities is always incorporated to ensure data collection and realtime on-demand access to relevant data to identify and solve a problem even in remote areas.
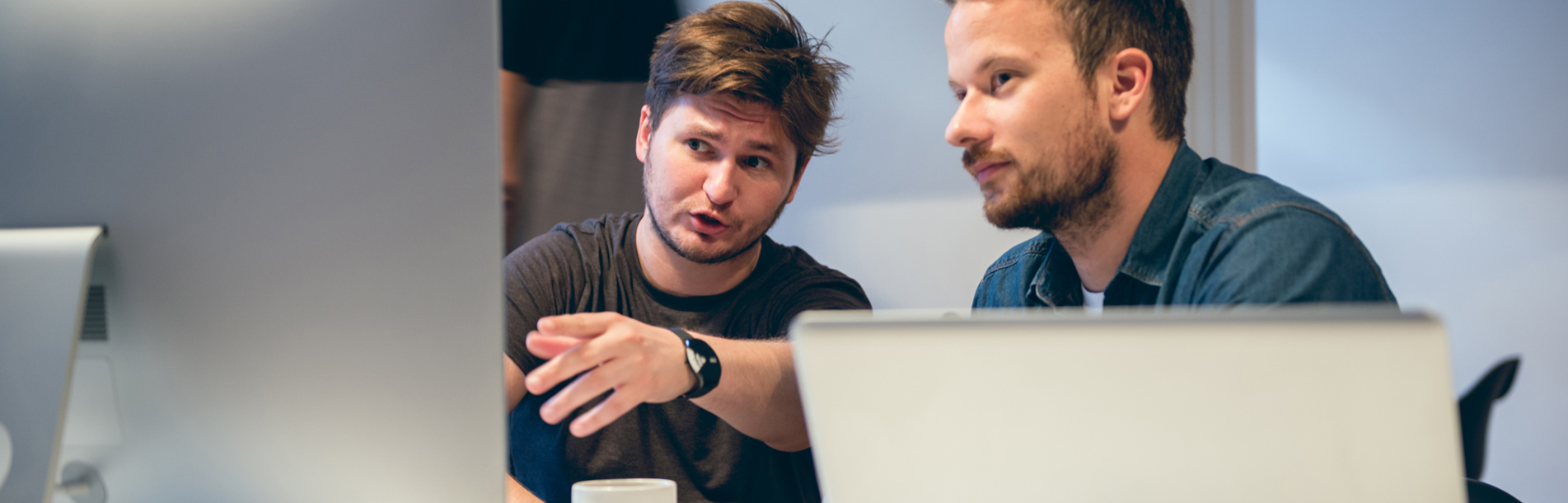
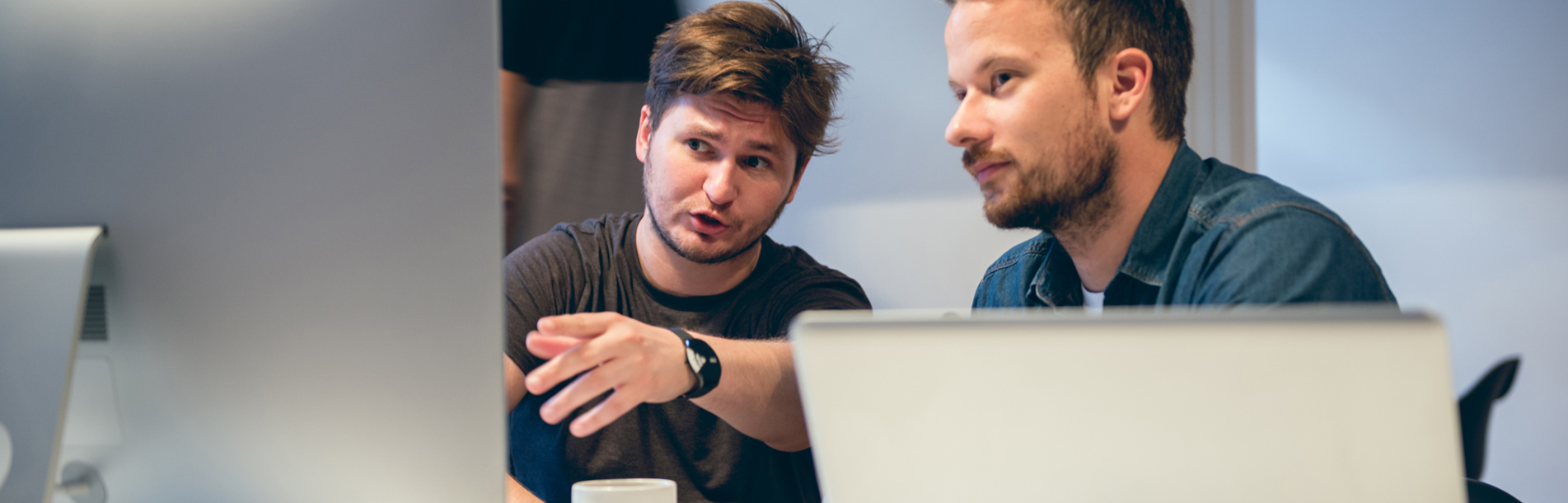